IT-Matex III with Counting Scales
Kobayu Co. Ltd.
LogisticsInventory Management System Helps Prevent Shipping Errors and Increase Work Efficiency
Kobayu Company Ltd. introduced an inventory management system to help prevent shipping errors, such as shipping of the wrong parts or the wrong number of parts. This case study describes how combining IT-Matex III with counting scales and other peripheral equipment realizes a system that is helping to resolve shipping issues and increase work efficiency at the company.
The Challenge
Kobayu Company Ltd. is a general trading company that specializes in screws, offering over 10,000 different products. The company prides itself in providing detailed and conscientious service, accepting orders of even a single screw and offering delivery times as short as one day. Kobayu manufactures screws, bolts, rivets, and machined products that are used across a broad spectrum of industries, including automotive, precision equipment, and electrical, to name but a few. Among the products the company offers there a many items that are only fractionally different in length, and so cannot be distinguished by their appearance. However, delivering the wrong part can lead to very serious problems for the customer, so it is extremely important that the correct screws in the correct numbers are delivered.
The company had tried a variety of measures to prevent shipments with wrong parts or part counts from going out, but had not been very successful. They decided that they needed to drastically rethink their approach and began to consider the introduction of a barcode-based inventory control system.
Our Solution
IT-Matex III
Counting Scales
Benefits
After spending one year looking at suppliers and then another six months observing and examining case studies, Kobayu decided on the IT-Matex III Inventory Management System from DIGI. It took an additional year to tailor the system to Kobayu’s needs.
A wireless LAN connects the IT-Matex III system to some 19 mobile terminals, 13 counting scales, and 6 label printers at the company, and picking is done using a dedicated cart. Small-size bags are used for filling small lot orders. However, for larger lots, a counting scale on the picking cart is used together with a count error prevention program, to make sure there is no mistake in the part count. Additionally, when the order form barcode is scanned, the order data is automatically reflected in the sales data, which helps reduce input errors for business tasks that are outside the inventory management area.
By introducing IT-Matex III, Kabayu is able to monitor order fulfillment and inventory status on a constant basis and has succeeded in drastically reducing shipping errors. They have also been able to significantly shorten overall work time and increase work efficiency.
Customer Profile
Company: | Nihon Kolmar Co., Ltd. |
---|---|
Country: | Japan・Osaka |
Website: | http://www.kobayu.co.jp/ |
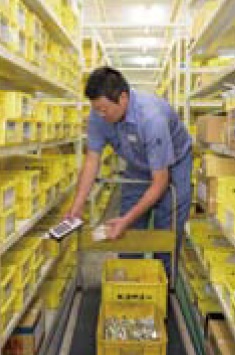
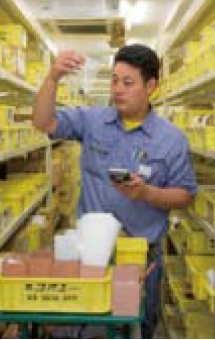
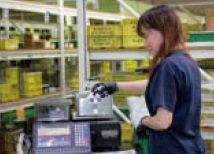
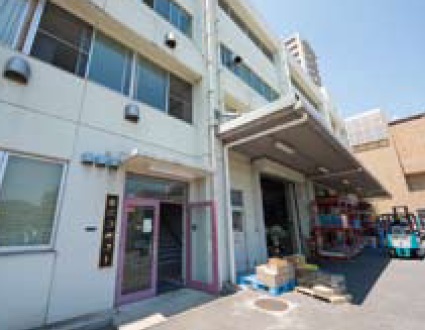